Optimized & Industry-ready Solutions
For All Your Complicated Needs
We offer a premium fast track delivery option to enable us to supply against time restricted contracts with ease. Giving the flexibility to choose a standard or priority completion time whilst sustaining our high quality
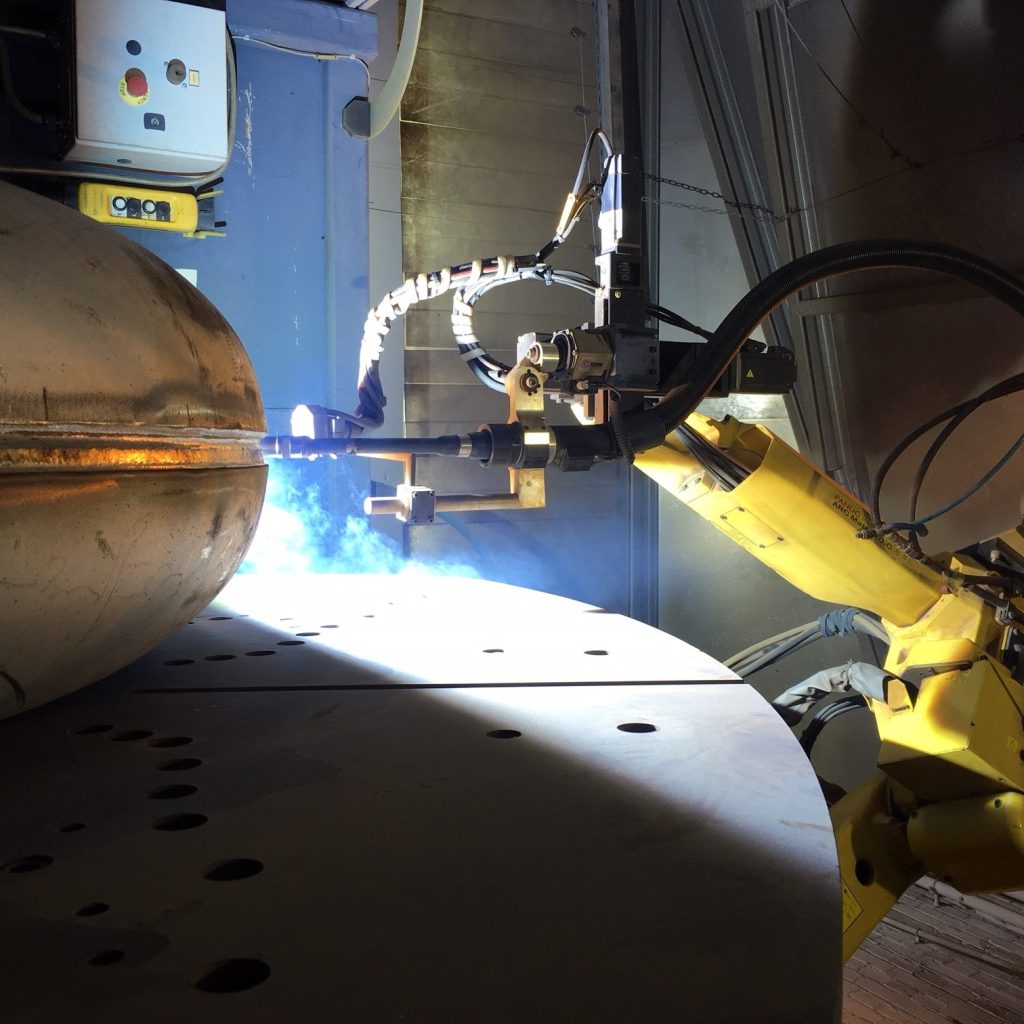
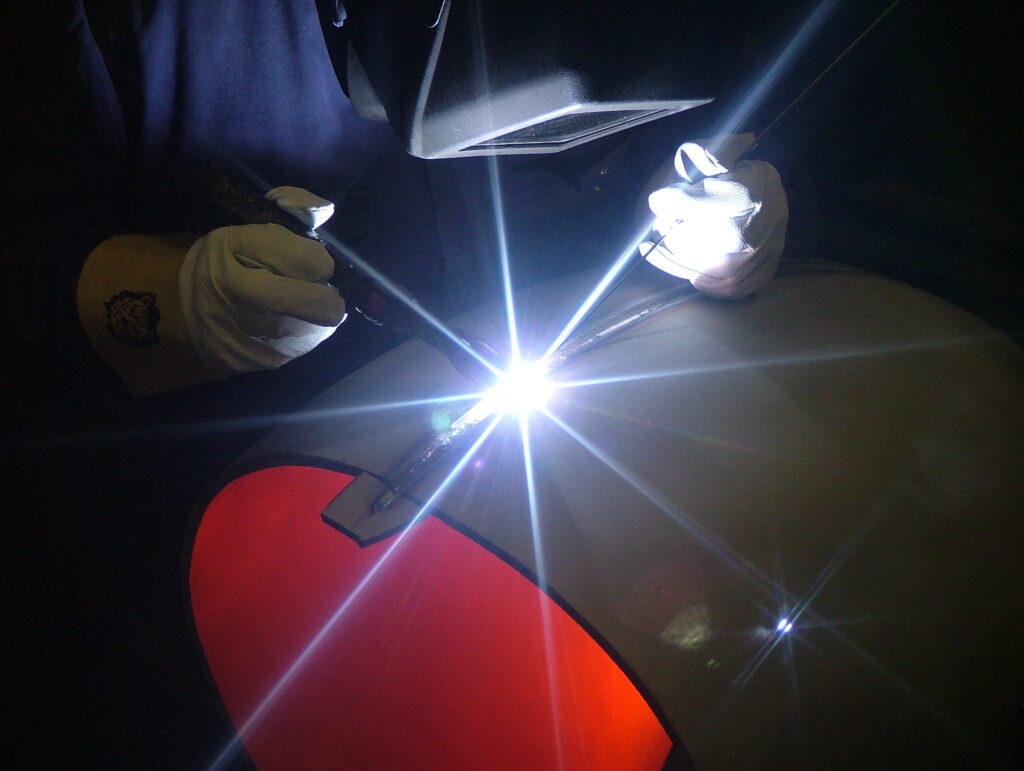

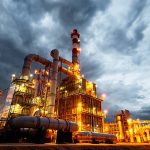
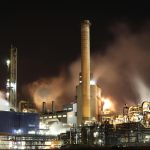
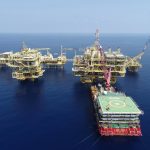
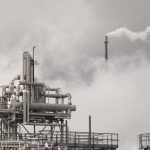
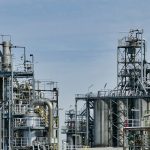
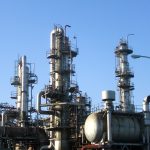
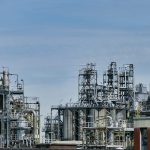
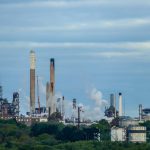
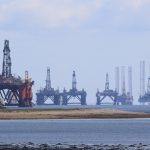
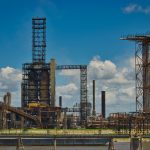
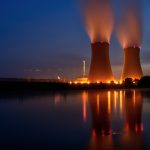
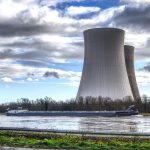
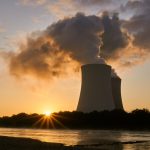
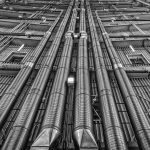
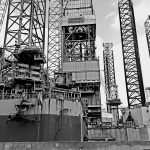
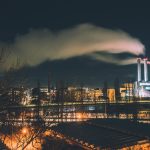

Our Innovations
Industry Grades
Steel Grade 304 / 304L | UNS S30400 / UNS S30403 | 1.4301 / 1.4307
These types of steel are some of the most regularly specified and have come to represent the embodiment of the basic stainless product. They are part of the 300 Series of steels (as defined in SAE specifications) which covers a range of austenitic chromium-nickel alloys. They are also known as 18/8 stainless due to their chemical composition which includes approximately 18% chromium and 8% nickel by weight. The steels are easy to form, weld, and fabricate and their resistance to corrosion from, amongst other things, acids naturally contained in food has resulted in them being used widely in the food and drink processing industries.
Type 304 and Type 304L have very similar chemical and mechanical properties and are often included on a single material test certificate when the actual properties of a stainless steel plate meet the criteria of both types. This is a very common occurrence. Type 304L is a variation of Type 304 and has a lower carbon content which improves weldability and lowers the risk of reduced corrosion resistance around the weld. Type 304L also has a slightly lower yield and tensile strength than Type 304.
As with most steel plate products a number of different designations are used for these steels. The most common are:
•Type 304 1.4301 (EN Steel Number) S30400 (UNS)
•Type 304L 1.4307 (EN Steel Number) S30403 (UNS)
Typical industrial sectors:
•Food Processing
•Chemical Industry
•Brewing
•Pharmaceuticals
•Petrochemicals
Typical product applications:
•Heat Exchangers
•Pipelines
•Pressure Vessels
•Flanges and fittings
•Valves
•Condensers.
Duplex | UNS S31803/S32205 | 1.4462Duplex stainless has a microstructure which is split roughly 50:50 between austenite and ferrite and balancing of these phases provides the following benefits:•Higher strength which is around twice that of Type 304 austenitic stainless steel. This leads to reduced plate thicknesses being used in fabrications reducing the weight which is of particular significance in items such as pressure vessels, storage tanks, and structural applications such as bridges.• Good weldability in thick plates .•Good low temperature toughness. •Resistance to stress corrosion cracking of importance in many applications including hot water tanks, process plant, brewing tanks, and desalination plant .Another key feature of Duplex stainless is its enhanced corrosion resistance. There is no single measure of corrosion resistance but the Pitting Resistance Equivalent Number (PREN) is widely used as a means of comparing the relative corrosion resistance of different steel grades. The PREN is obtained by applying a mathematical formula to the chemical composition of a steel so that PREN = %Cr + (3.3 x %Mo) + (16 x %N). Using this formula 31803 Duplex stainless has a PREN of 35 which when compared with the PREN of Type 304 and Type 316 (18 and 24 respectively) demonstrates its superior corrosion resistance. In short, due to its higher strength, longer component life cycle, and lower alloy composition, Duplex stainless can be a very cost effective solution to an engineering problem.
Super Duplex | UNS S32750 | 1.4410Super Duplex UNS S32750 has excellent corrosion resistance in a wide variety of corrosive media making it ideal for use in environments exposed to the harshest chemical conditions. It has outstanding resistance to pitting and crevice corrosion in seawater and other chloride containing environments, with Critical Pitting Temperature exceeding 50°C.Compared to austenitic and 22%Cr duplex stainless steels, UNS S32750 is of higher strength and even more suitable in situations where it will be exposed to extremely high stresses. This combined with its excellent ductility and impact strength at both ambient and sub-zero temperatures further increases its appeal as the ultimate super duplex grade. High resistance to abrasion, erosion and cavitation erosion combined with excellent resistance to stress corrosion cracking in chloride containing environments makes UNS S32750 perfect for use in the Oil and Gas Industries where subsea equipment is subject to some of the harshest chloride containing conditions in the world. UNS S32750 is listed in NACE MR 01 75 for sour service for its suitability of use for oilfield equipment where sulphide stress corrosion cracking may be a risk in hydrogen sulphide (sour) environments .UNS S32750 is also ASME Approved for Pressure Vessel applications. Typical industrial sectors:• Chemical Process Industry• Marine Industry and Shipbuilding• Oil and Gas Industry• Pollution Control• Pulp and Paper Industry• Food Industry• Agrochemicals• Civil Engineering
S31254 Stainless Steel
Grade 6 Moly | UNS S31254 | 1.4547
Stainless steel grade S31254 is a very high end austenitic stainless steel.
For certain applications, grade S31254 has been reported to be a cost-effective substitute for high nickel and titanium alloys.
It is designed with a combination of impact toughness resistance to chloride stress corrosion cracking, and pitting and crevice corrosion with strength that is twice that of the stainless steel 300 series.
It is known to possess excellent workability as well.
As with most steel plate products a number of different designations are used for these steels. The most common are:
•Type SMO 254 1.4547 (EN Steel Number) S31254 (UNS)
Typical industrial sectors:
• Saltwater handling
• Tall oil distillation columns
• Flue gas desulphurization scrubbers
• Components used in petroleum production
• Food processing equipment
• Process equipment in chemical industry
• Bleaching equipment in the pulp and paper industry
• Flue-gas cleaning
• Desalination
• Heat exchangers
321 / 321H Stainless Steel
Grade 321 / 321H | UNS S32100 / UNS S32109 | 1.454 / 1.4878
Characterised by its good oxidation resistance up to 1600F and its superior resistance to polythionic stress corrosion cracking 321 Stainless is an alloy that offers outstanding performance at a competitive price.
Alloy 321 stainless is a titanium stabilized grade commonly used for service in the 1000-1600°F temperature range.
For service temperatures up to about 1600°F, a stabilizing treatment at 1550-1650°F, air cool, may be used to provide optimum resistance to intergranular corrosion and to polythionic acid stress corrosion cracking. 321 stainless is readily welded by all common methods including submerged arc. Appropriate weld fillers are AWS ER347 bare wire and E347 covered electrodes.
321 stainless is similar in machinability to 304 stainless steel. It has a machinability rating of 45% relative to AISI B1112.
Features of Alloy 321
Oxidation resistant to 1600°F
Stabilized against weld heat affected zone (HAZ) intergranular corrosion
Resists polythionic acid stress corrosion cracking
As with most steel plate products a number of different designations are used for these steels. The most common are:
•Type 321 1.4541 (EN Steel Number) S32100 (UNS)
•Type 321H 1.4878 (EN Steel Number) S32109 (UNS)
317L Stainless Steel
Grade 317L | UNS S31703 | 1.4438
Alloy 317L is a molybdenum containing, low carbon austenitic stainless steel with increased additions of chromium, nickel, and molybdenum for better corrosion resistance and increased resistance to chemical attack for sulphurous, acetic, formic, citric, and tartaric acids.
Due to its low carbon content, 317L also provides resistance to sensitization when welded and higher creep, stress to rupture, and tensile strength at elevated temperatures.
It is non-magnetic in the annealed condition but may become slightly magnetic after welding.
Alloy 317L is commonly used to handle sulphur, pulp liquor, acid dyestuffs, acetylating and nitrating mixtures, bleaching solutions, severe coal and oil, and many chemical compounds.
Corrosion Resistance
•Demonstrates superior corrosion resistance in difficult environments including a wide range of chemicals, especially in acidic chloride environments
•Excellent resistance in applications where contamination is desired to be kept to a minimum
•Low carbon content allows 317L to be highly resistant to intergranular corrosion
•Combats the tendency to pit when in contact with phosphorus acids, chlorides, bromides, and iodides
Heat Resistance
•All chromium-nickel-molybdenum steels all have excellent resistance to oxidation
•Demonstrates a low rate of scaling in ordinary atmospheres at temperatures up to 1600-1650°F (871-899°C).
As with most steel plate products a number of different designations are used for these steels. The most common are:
•Type 317L 1.443 (EN Steel Number) S31703 (UNS)
Typical industrial sectors:
•Paper and pulp handling equipment
•Chemical and petrochemical processing equipment
•Condensers in fossil and nuclear fueled power generation stations
•Food processing equipment
•Textile equipment
904L Stainless Steel
Grade 904L | UNS NO8904 | 1.4539
Alloy 904L (UNS N08904) is a super austenitic stainless steel that is designed for moderate to high corrosion resistance in a wide range of process environments.
The combination of high chromium and nickel content, coupled with additions of molybdenum and copper, assures good to excellent corrosion resistance.
With its highly alloyed chemistry , 25% nickel and 4.5% molybdenum, 904L provides good chloride stress corrosion cracking resistance, pitting and general corrosion resistance superior to 316L and 317L molybdenum enhanced stainless steels.
Alloy 904L was originally developed to withstand environments containing dilute sulphuric acid.
It also offers good resistance to other inorganic acids such as hot phosphoric acid as well as most organic acids.
Applications
===========
• Air Pollution Control — scrubbers for coal-fired power plants
• Chemical Processing — process equipment for the production of sulphuric, phosphoric, inorganic and organic acids and the production of phosphate-based fertilizers
• Metallurgical Processing — pickling equipment using sulphuric acid
• Oil and Gas Production —offshore process equipment
• Pharmaceutical Industry — process equipment
• Pulp and Paper — processing equipment
• Seawater and Brackish Water — condensers, heat exchangers and piping systems
Alloy 276
Alloy C276 | UNS N10276 | 2.4819
Alloy C-276 is an improved wrought version of Alloy C and has the same excellent corrosion resistance as that material but has greatly improved fabricability.
It can be hot worked and cold formed by conventional procedures.
It can be joined by all of the common welding methods and resists the formation of grain boundary precipitates in the weld-affected zone, thus making it suitable for most chemical process applications in the aswelded condition.
It resists pitting and stress-corrosion cracking and is resistant to oxidation at temperatures up to 1900 deg.F.
DESIGN FEATURES
==============
• Outstanding corrosion resistance and oxidizing environments.
• Excellent resistance to pitting and stress-corrosion cracking.
• Maintains corrosion resistance in welded joints
Typical industrial sectors:
• Chemical processing
• Pollution control Pulp and paper
• Other severe environments and/or conditions.
Alloy 800
Alloy 800 | UNS N08800 | 1.4876
Alloy 800 is a widely used material of construction for equipment that must resist corrosion, have high strength or resist oxidation, carburization and other harmful effects of high-temperature exposure.
For high temperature applications requiring optimum creep and rupture properties Alloy 800HP is used.
The Chromium in the alloy imparts resistance to oxidation and corrosion.
The high Nickel content maintains an austenitic structure so that the alloy is ductile.
The Nickel also contributes resistance to scaling, general corrosion and stress corrosion cracking.
The iron content provides resistance to internal oxidation.
Good creep-rupture properties at temperatures above 600 deg. C (1110 deg. F) without loss of ductility during long term use at temperatures below 700 deg. C (1290 deg. F), due to limitation of (Ti & A) content to max 0.7%. However, by using 800HP with increased (Al & Ti) content to 1.2%, temperatures above 700 deg. C (1290 deg. F) can be achieved.
Good resistance to reducing oxidizing and nitriding atmospheres and to atmospheres which alternates between reducing and oxidizing conditions.
Metallurgical stability in long-term applications at high temperatures.
Typical industrial sectors:
• Steam / hydrocarbon reforming
• Ethylene pyrolysis tubing
• Ethylene dichloride cracking tubes
• Components, eg. Heat exchangers, piping systems, etc
• Steam generators tubing in helium coolant, high temperature reactor systems
Alloy 800 H/HT
Alloy 800 H/HT | UNS N08810 & N08811 | 1.4958 & 1.4959 are solid solution strengthened, iron-nickel-chromium alloys, typically offered as one, dual certified alloy meeting the elemental requirements of both alloys. The principle difference between alloy 800H and 800HT® material is the restricted aluminium and titanium content in 800HT®, which results in higher creep and stress rupture properties. Both Alloy 800H and 800HT® are superior to Alloy 800 (UNS N08800), having greater creep and stress rupture properties. The alloy is typically used for applications involving long-term exposure to high-temperatures where resistance is needed from oxidation, carburization and other types of high-temperature corrosion. Hydrocarbon processing, heat-treat furnaces and power generation are some of the most common applications where 800H & 800HT® is utilized. Pressure vessels and vessel components constructed from 800H and 800HT® are approved under the ASME, Boiler and Pressure Vessel Code, Section VIII, Division 1.
High nickel and chromium contents in both alloy 800H and 800HT® result in excellent resistance to oxidation, carburization and sulfidation. The high nickel content also increases the resistance to nitriding, although not as good as other alloys such as Alloy 600, which contains a higher percentage of nickel.
Typical industrial sectors:
• Steam / hydrocarbon reforming
• Ethylene pyrolysis tubing
• Ethylene dichloride cracking tubes
• Components, eg. Heat exchangers, piping systems, etc
• Steam generators tubing in helium coolant, high temperature reactor systems
Grade 316 / 316L | UNS S31600 / UNS S31603 | 1.4401 / 1.4404
These steels are the second most regularly specified stainless steels after Type 304 and are part of the SAE defined 300 Series which encompasses a range of austenitic chromium-nickel alloys. Austenitic stainless steels like Type 316 are widely available, have good general corrosion resistance, good cryogenic toughness, and excellent formability and weldability.
Type 316 has 2-3% Molybdenum included in its chemical composition which prevents specific forms of corrosion and generally enhances its corrosion resistance. Type 316 is often referred to as “marine grade” stainless due to its increased resistance to chloride corrosion compared to Type 304 making it a very suitable material for use in salt water environments.
Type 316L is a variant of Type 316 and differs by having a lower Carbon content as well as slightly lower yield and tensile strengths. Type 316L offers improved weldability and also reduces the possibility of lower corrosion resistance around welded areas.
As with most steel plate products a number of different designations are used for these steels. The most common are:
•Type 316 1.4401 (EN Steel Number) S31600 (UNS)
•Type 316L 1.4404 (EN Steel Number) S31603 (UNS)
Typical industrial sectors:
•Brewing
•Chemical Industry
•Dairy
•Food processing
•Marine equipment
•Petrochemicals
•Pharmaceuticals
Typical product applications:
•Condensers
•Heat Exchangers
•Filters
•Pressure Vessels
•Valves
•Flanges and Fittings
Zeron 100 | UNS S32760 | 1.4501
Super Duplex Alloy UNS S32760 (F55 / 1.4501) has excellent corrosion resistance to a wide variety of media, with outstanding resistance to pitting and crevice corrosion in seawater and other chloride containing environments, with Critical Pitting Temperature exceeding 50°C.
Providing higher strength than both austenitic and 22% Cr Duplex Stainless Steels UNS S32760 (F55) is suited to a variety of applications in industries such as Chemical Processing, Oil & Gas, and Marine environments.
UNS S32760 (F55 / 1.4501) is listed in NACE MR 01 75 for sour service and having gained ASME Approval for Pressure Vessel applications.
Typical industrial sectors:
• Chemical Process Industry
• Marine Industry and Shipbuilding
• Oil and Gas Industry
• Pollution Control
• Pulp and Paper Industry
• Food Industry
• Agrochemicals
• Civil Engineering
310S Stainless Steel
Grade 310S | UNS S31008 | 1.4845
Alloy 310S displays excellent resistance to oxidation under mildly cyclic conditions to 1100°C. Due to its high chromium and medium nickel content, 310S has good resistance to sulfidation and other forms of corrosion.
Alloy 310S is widely used in moderately carburizing atmospheres such as those encountered in petrochemical environments. 310S is not suggested for the severe thermal shock of repeated liquid quenching.
310S is often used at cryogenic temperatures, with excellent toughness to -268°C and low magnetic permeability. 310S has a machinability rating of 42% relative to AISI B1112 steel.
Features of Alloy 310S
* Oxidation resistance to 2000°F
* Moderate strength at high temperature
* Resistance to hot corrosion
* Strength and toughness at cryogenic temperatures
As with most steel plate products a number of different designations are used for these steels. The most common are:•Type 310S 1.4845 (EN Steel Number) S31008 (UNS)
347/H Stainless Steel
Grade 347 | UNS S34700 | 1.4550
Type 347 stainless steel has slightly improved corrosion resistance over type 321 stainless steel in strongly oxidizing environments.
Type 347 is stabilized with columbium, it is preferable for aqueous and low temperature environments due to its good resistance to intergranular attack.
Both 347 and 321 offer good resistance to polythionic acid stress corrosion cracking, encountered in oil refineries.
The high temperature oxidation resistance of 347 is similar to that of 304 stainless steel. Useful to 1500°F.
Often in many product forms, the grain size and carbon content can meet both the 347S and 347H requirements.
Appropriate weld fillers are AWS ER347 bare wire and E347 covered electrodes.
Features
•Good creep strength up to 1500°F
•Maintains good corrosion resistance in applications where the temperature is between 800°F and 1500°F.
•Good resistance to intergranular corrosion in the as welded condition.
As with most steel plate products a number of different designations are used for these steels. The most common are:
•Type 347 1.4550 (EN Steel Number) S34700 (UNS)
Typical industrial sectors:
•Oil Refineries
•Fluid catalytic cracking units (FCC)
•Hanger rods
•Recuperator tube sheets, shell, supports
•Especially where temperatures exceed 550°F and resistance to sulfidation is needed
•Fired heater tubes
•Distributor trays and thermowells
•Equipment in and around reactors (good resistance to polythionic acid)
5083-0 Aluminium
Alloy 5083 aluminium plates have higher strength than 5052 plate and has exceptional thermal conductivity.
The tempered condition, it retains good formability due to excellent ductility.
It is highly suitable for welding and can be hardened by cold work.
Because Alloy 5083 exhibits excellent resistance to general corrosion, it is used in marine applications.
Since Alloy 5083 is capable of withstanding extremely low temperatures without brittleness or loss of properties, it is especially suited to the cryogenic market.
Typical industrial sectors:
•LNG ship construction
•Pressure vessels
•Storage tanks
•Welded structures (high strength)
•Armour plate
•Drilling rigs
6061 Aluminium
6061 aluminium is an American alloy and the most versatile of the heat-treatable alloys.
Typical Use
Widespread use of the alloy includes the production of heavy-duty structures. It is a medium to high strength heat-treatable material with improved corrosion resistance and medium fatigue strength. 6061 aluminium, in the annealed condition, offers excellent weldability and formability, and is readily disposed to furnace brazing.
Specifics
6061 commercial aluminium alloy offers medium to high strength. It is a heat treatable alloy with medium fatigue strength and very good corrosion resistance. It is typically used in heavy duty applications.
Typical Applications
Commercial applications for this engineering material include:
Motorboats
Aircraft structures
Shipbuilding
Truck bodies
Pylons & towers
Rail coaches
Alloy 200/201
Alloy 200/201 | UNS N02200/N02201 | 2.4066/2.4068
Alloy 200 & Alloy 201 are nickel alloys which have been combined into one with dual certified chemistry.
This means that you receive the required characteristics from both alloys in a single solution.
Alloy 200/201 offers exceptional resistance to caustic alkalis and good mechanical properties over a wide temperature range.
The alloy is used in such applications as fluorine and sodium hydroxide production as well heat exchangers and pressure vessels.
Key Features:
Alloy 200 / 201 is similar in strength to mild steel in the annealed condition.
The alloy offers exceptional resistance to caustic alkalis and good corrosion resistance in neutral and moderately reducing environments.
Alloy 200/201 displays good mechanical properties over a wide temperature range.
Typical industrial sectors:
•Food processing
•Fluorine generation
•Heat exchangers
•Tank heads
•Chemical processing & storage
•Phenol storage & transportation
•Sodium hydroxide production
•Pressure vessels & vessel components
Alloy 400
Monel® 400 | UNS N04400 | 2.4360
Monel 400 (NA13, N04400) is a nickel-copper alloy with good strength and excellent corrosion resistance in a range of media especially sea water, hydrofluoric acid, sulfuric acid, and alkalis.
Although the grade can be tempered or cold worked to increase its properties, Monel 400 (2.4360) is supplied in the annealed condition as standard.
Monel 400 / NA13 is used for marine engineering, chemical and hydrocarbon processing equipment, valves, pumps, shafts, fittings, fasteners, and heat exchangers.
In the annealed condition Monel 400 / N04400 is an alloy that is easy to form and fabricate with no requirements for additional heat treatments to re-balance the alloy.
Typical industrial sectors:
•Food processing
•Fluorine generation
•Heat exchangers
•Tank heads
•Chemical processing & storage
•Phenol storage & transportation
•Sodium hydroxide production
•Pressure vessels & vessel components
Alloy 600
Monel® 600 | UNS N06600 | 2.4816
INCONEL® alloy 600 is combination of Nickel Chromium and Iron provides a standard material for the chemical industry and the automotive engine, aeroengine and airframe sectors.
Controlled chemical composition limits are applied in the nuclear industry to eliminate the risk of stress corrosion cracking by high purity water containing chloride ions.
From its introduction to industry in the 1930’s the alloy has developed into a wide spectrum of applications for high temperature strength and corrosion resistance.
A widely used thermocouple sheath material in carbon or nitrogen rich atmospheres the alloy continues in use as an excellent muffle construction material and is also used for jigs and fixtures in heat treatment processes.
Controlling the compositional limits and correctly processing and thermally annealing the material is essential to avoid pitting and the risk of stress corrosion cracking in some service environments.
Typical industrial sectors:
• Chemical industry
• Aerospace
• Heat treating industry
• Pulp and paper industry
• Food processing
• Nuclear Engineering
• Gas turbine components
Alloy 625
Inconell® 625 | UNS N06625 | 2.4856
INCONEL® 625 alloy is used for its high strength, excellent fabricability (including joining), and outstanding corrosion resistance. It has become a standard material of construction in a wide variety of industrial applications, which is unusual for an alloy. Alloy 625 is valuable in that it is versatile and able to solve a wide variety of design and application problems.
INCONEL® 625 alloy consists of a solid solution alloy of nickel, chromium and molybdenum alloy with niobium added. When this combines with molybdenum it distorts the alloy’s atomic matrix, thus providing particularly high strength in the annealed condition without a deliberate strengthening heat treatment. This combination of elements creates superior resistance to a wide range of corrosive environments of unusual severity.
Alloy 625 is generally supplied in the annealed condition, to provide utmost stability during fabrication and subsequent service. INCONEL® 625 alloy has found to have a resistance to potable and salt or brackish water, where Chloride ions cause pitting and crevice corrosion to become established. As a result, pipelines for gathering sour gas have been built with solid (or clad) INCONEL® 625 alloy and used in
seawater heat exchangers in refineries, power plants, and offshore topside services that often need this material.
Additionally, the alloy’s properties make it an excellent choice for sea-water applications, including freedom from local attack (pitting and crevice corrosion), high corrosion-fatigue strength, high tensile strength, and resistance to chloride-ion stress-corrosion cracking.
The outstanding and versatile corrosion resistance of INCONEL 625 alloy under a wide range of temperatures and pressures is a primary reason for its wide acceptance in the chemical processing field. Because of its ease of fabrication, it is made into a variety of components for plant equipment.
Typical industrial sectors:
• Oil extraction
• Oil refining
• Aerospace
• Automobile
• Marine
• Heat treating industry
• Pulp and paper industry
• Waste treatment
Alloy 825
Alloy 825 | UNS N08825 | 2.4858
Alloy 825 is a Nickel-iron-chromium alloy with additions of molybdenum, copper and titanium.
The alloys chemical composition provides exceptional resistance to many corrosive environments.
The Nickel content is sufficient for resistance to Chloride-ion stress corrosion cracking.
The nickel, combined with molybdenum and copper, also gives outstanding resistance to reducing environments such as those containing sulfuric and phosphoric acid.
The molybdenum also aids resistance to pitting and crevice corrosion.
The alloys Chromium content confers resistance to a variety of oxidizing substances such as nitric acid, nitrates and oxidizing salts.
The titanium addition, with appropriate heat treatment, will stabilize the alloy against sensitization to intergranular corrosion.
Good resistance to stress corrosion cracking.
Satisfactory resistance to pitting and crevice corrosion.
Good resistance to oxidising and non-oxidising hot acids.
Good mechanical properties at both room and elevated temperatures up to approximately 550 deg. C (1020 deg. F).
Permission for pressure-vessel use at wall temperature up to 425 deg. C (800 deg. F).
Typical industrial sectors:
• Components such as heating coils, tanks, crates, baskets and chains in sulfuric acid pickling plants
• Fuel element dissolvers
• Sea water cooled heat exchangers
• Pipelines carrying wet sulphur dioxide gas and pulp digesters in the papermaking process
• Heat exchangers
• Evaporators
• Scrubbern
• Air cooled heat exchangers